"You didn't realize that we make the most beautiful tile in the world in Spokane, did you?" Fireclay CEO Eric Edelson says by phone from the Bay Area. It's true. Since October 2022, all of the company's pressed clay and glass tiles have been made at the former Quarry Tile plant in northeast Spokane. In fact, the Spokane location is the only manufacturer of glass tiles in the United States, Edelson says. The company's California locations use different production methods for other types of tiles.
Fireclay was founded in 1986 with a couple of small factories in California that sold to other retailers. Edelson took the reins 16 years ago. "In 2013, we actually fired all of our customers, all of our retail accounts, and decided to go direct. And we started using the internet and social media to really just bring our products directly to architects and designers and homeowners. And that led to tremendous growth."
A need for more manufacturing capacity led to a search for another factory, ending with the purchase of Spokane-based Quarry Tile. "No one in Spokane really knew it existed because their model was to manufacture for other companies and allow those companies to resell," Edelson says, noting that the 120,000-square-foot Spokane plant is actually a lot larger than their California locations.
Fireclay now has eight showrooms, after opening five in 2024, including its first East Coast shop in New York City's Flatiron District and one in Santa Monica. The Spokane showroom is scheduled to reopen sometime in 2025, though curious shoppers can already stop by to see tile samples in the factory lobby.
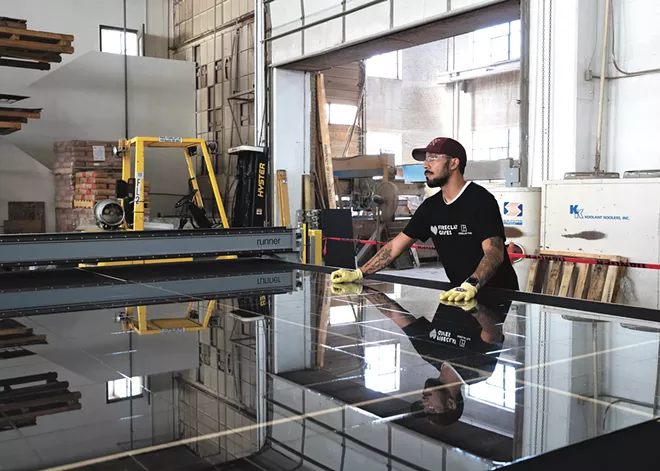
Gerald Havens oversees operations at the Spokane plant, which can turn out a finished tile from the pile of locally sourced raw clay in just 90 minutes. After mixing the raw material with plenty of water in the equivalent of a massive KitchenAid, the resulting very runny mixture is quick-dried into a fine powder. The powder is then tightly compressed into molds with the resulting tiles hustled off on a conveyor belt for firing in a 42-meter-long natural gas kiln. After glazing is applied, the tiles are fired once more, then carefully packed for shipment.
Crafting glass tiles is a different process entirely. Large sheets of plate glass float on a cutting table where they're carefully scored and expertly cracked apart into smaller tiles, which are then individually screenprinted with ink. A trip through the kiln softens the tiles' sharp cut edges into smoothly curved, elegant pieces.
Whatever the tile type, 90% of Fireclay's production is made to order.
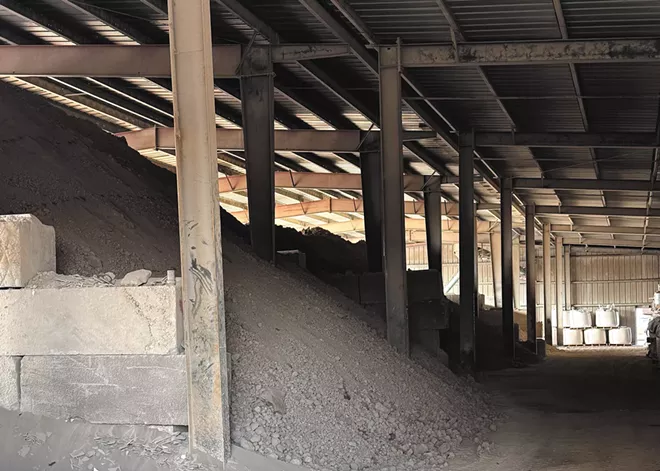
"We offer design services and then make your tile exactly the way you want it," Edelson says. "We like to say our story starts with yours... When you work with us and we make something for you, it's one of a kind. We're making it exactly for you, and we do that at scale for 1,000 customers a month."
Havens says in addition to an assortment of in-stock tile colors, the plant can create custom color-matches and mosaics at various price points. He assists customers with a sample "chip box" of tiles — including, glass, pressed clay or brick options. Completing an order that's custom-color matched can take a few weeks as customers will receive a sample for approval prior to placing the final order.
"We work with everyone and anything. It's the retiree who wants to do a little spruce up of their kitchen backsplash all the way up to a boutique hotel where we're doing every bathroom. We're part of national rollouts for Starbucks or corporate customers like Salesforce or Google or Meta," Edelson says, noting Fireclay tile is featured at the Spokane Airport. "We work with the most discerning, highest-end clients across the country, but we also make ourselves available to everyone via the internet."
As a certified B-corporation, Fireclay is part of a growing number of companies, including Ben & Jerry's and Patagonia, that endeavor to embody the philosophy that business can be a force for good. The certification process takes place every three years and is exacting, "like a root canal on your business," Edelson says. "It's really looking at every facet of your company, from your corporate governance to how you treat your team and your employees to what you do for the environment, how you show up for your community, and the support you provide your local community, and how you treat your customers." The company is 30% employee-owned, something that has been a new experience for the Spokane-based crew, Edelson says. "It's been a really fun journey helping the Spokane team members understand what it means to be an owner, to understand what it means to have a say."