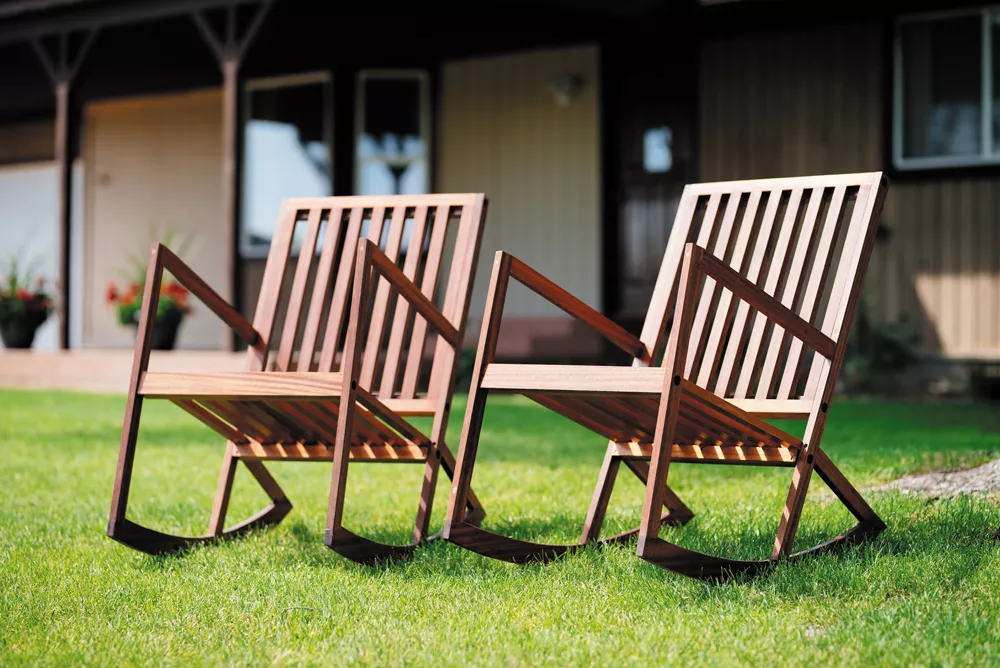
From acacia to ziricote, tree wood has been prized for millenia for its use in building everything from ships to structures and to fashioning functional objects like bowls and furniture to delightfully and strictly decorative applications. The grain, the sheen, the color, the texture — all these and more factor into the choices of the woodworker, whose legacy spans nearly every culture, time period and geographic region. Read on for insight into the inspiration and craftsmanship that go into locally made wooden objets d'art.
Cody Schuler
"Every block of stone has a statue inside it, and it is the task of the sculptor to discover it." — Michelangelo
The task for woodworker Cody Schuler is sussing out the perfect piece of wood for his custom dressers, desks, tables, chairs, keepsake containers and more.
For example, Schuler was in Portland picking up a slab of wood for a customer's table and happened upon an independent sawmill operator with a large inventory of wood.
"I spent a couple hours with him perusing maple rounds, but in my nosiness I found a stack of black walnut under a tarp, out of the way," says Schuler, who knew the stack contained the perfect wood for a different and no less important job — his mother's dinette.
Schuler got into woodworking in 2015. He'd graduated from college and was preparing to work in social services, though he explored woodworking as a creative release. Then three years ago, looking for a change for himself and his growing family, he started Pacific Carpentry as a more permanent endeavor and a new career.
"Two of our three kids were a part of the foster/adopt system, my wife was a therapist for families struggling with abuse and neglect, and I was a social worker investigating abuse and neglect cases," says Schuler, who felt that social work wasn't the best fit for him anymore and decided to start his own business. He then spent several months cold-calling contractors and homebuilders looking for work.
One of his first jobs came from a former Child Protective Services colleague, Theresa Forshag, who commissioned a large toy chest for the nursery in her home. The nursery is used for medically fragile foster babies until they're healthy enough to go to another foster home, Schuler explains.
"The toy chest was left up to my own design and is a large box made from flamed birch wood, with entirely hand-cut dovetail joinery — over 30 joints, cut strictly with hand tools — and interior walnut accents."
Now, Schuler works out of a 1,400-square-foot shop at his home northwest of Orchard Prairie. He employs hand tools such as planes, chisels, saws and rasps, as well as power tools like saws, sanders and a lathe, and importantly, he has a dust collection system. Finishing is done in a separate space.
"My business is pretty much a 50-50 split between heirloom furniture making and production trim work — hanging doors and windows, installing cabinets, and installing baseboards, casings, and crown molding," says Schuler.
Schuler has an old school approach to working: His plans start with graph paper, a ruler, a protractor and lots of notes.
Next he builds a prototype, typically with medium-density fiberboard (MDF) to help him flesh out his concept and avoid costly mistakes with the real wood, he says. Sometimes Schuler uses the model as a cutting template.
Joining methods depend on what he's building. For weight-bearing furniture like chairs and bed frames, he uses mortise (a recess in the wood) and tenon (the protruding piece that fits into the recess) joinery. For artistic pieces like keepsake boxes and frames, Schuler uses an ancient technique called dovetailing because the repetitive, interlocking shapes are visible (look inside an antique drawer to see an example of dovetail joints).
"In my opinion, joinery is where true heirloom furniture sets itself apart," Schuler says. "I've seen and owned plenty of furniture that looks great and is styled well for its environment, but as soon as it is put under stress, it will literally fall apart."
His goal is to create, design and manufacture his own furniture line, a project he's chipping away at, hoping to have it underway by summer 2022.
"When I make furniture, a primary goal is to create something that my customers feel is an investment — something that their great-great-grandchildren will still be able to use in their time," says Schuler.
See more of Cody Schuler's work at
www.pacificcarpentry.com.

CJ Morrison
CJ Morrison remembers being intrigued while watching her dad in his woodshop, but it wasn't until she was in Oklahoma, attending college and working in the food industry, that she explored woodworking herself. Her then-boyfriend had a carpentry background and an enviable woodshop, and together he and Morrison made mostly wall-hung artworks. To their surprise, their art resonated with art lovers.
By June 2015, the couple were making art full time. Two years later, Morrison relocated to Spokane — alone — bringing Roaming Roots with her.
Morrison works out of a 600-square-foot shop behind her West Central home. Her miter saw is a key tool for cutting the numerous angled pieces in her frames, shelves, trays, table tops and mosaic compositions that range from abstract to mountains and feathers. She uses a drill press for the plant propagation shelves she developed in 2020.
Her raw materials come from several sources, including repurposed wood from barns, fences, old lath strips and cabinet maker remnants. Her wood of choice is cedar.
"The grain pattern is so yummy if you know how to spot which boards have it," says Morrison, who also sells her work through From Here in River Park Square.
Her finishes vary, from opaque surfaces to translucent stains to bright colors with natural wood, and make for striking woodwork with a distinct contemporary vibe.
See more of CJ Morrison's work at
roamingrootswoodwork.etsy.com.
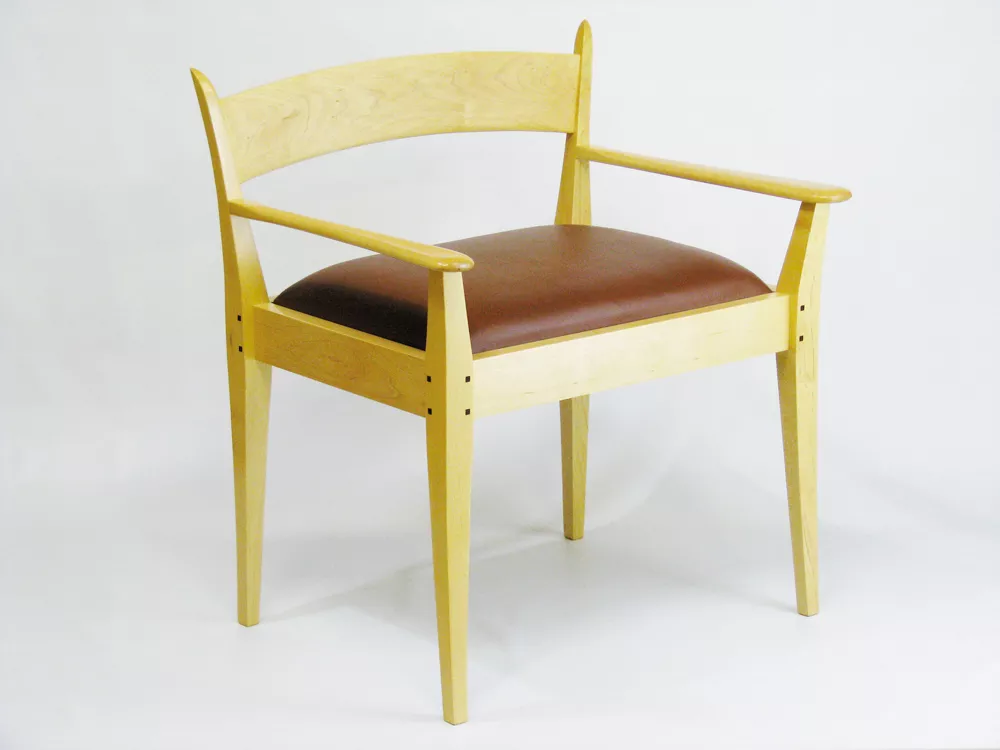
Dan McGrew
Shaker and Mission styles, and even Danish Modern all owe their appeal to the idea that "less is more," and that furniture is at its best when it is well-made and functional with minimal adornment.
That's the theme in much of longtime Spokane-based woodworker Dan McGrew's work. McGrew has spent the last 15 years or so building chairs, bar stools, dressers, tables, staircases, restaurant and bar fixtures, doors, and more.
"I got into woodwork as a kid in the '70s and made my share of crummy projects until figuring better ways of doing things later in life," says McGrew, who as a teenager worked for a contractor building custom homes.
McGrew finds inspiration in the designs by early American chair makers, as well as the Shakers. An offshoot of a Quaker religious group that emigrated from England in the late 1700s, the Shakers espoused a lifestyle of modesty and utilitarianism, which translated to solid wood furniture — versus using wood veneers — and no decoration. Their furniture is still popular today.
In addition to creating a barnwood table purchased by actor Viggo Mortensen, who you may know from his roles in Lord of the Rings and The Road, McGrew's commercial clients include Overbluff Cellars, Versalia Pizza, Inland Pacific Kitchen and the original Lantern Tavern in the Perry district (which became the Lantern Tap House, and is now the South Perry Lantern).
For the Lantern project, McGrew repurposed barnwood to create the cabinetry, using mortise and tenon joinery. He also created custom crown molding and integrated the tavern's sound system into the cabinetry.
McGrew repurposes his own scraps too.
"I like making modern chairs from the remnants of other projects," says McGrew, who works out of a 700-square-foot shop at his South Hill home. "They come out pretty cool, and it's a good use for all the little scraps."
Depending on the project, McGrew uses cherry, maple, both red and white oak, walnut, poplar, mahogany and sapele, an African import with properties similar to mahogany (Some species of mahogany are considered endangered).
Like many of the early American woodworkers he admires, McGrew does not use stains. Rather, he'll use six to eight coats of oil polyurethane depending on the wood species.
"Finishing can be a hard lesson to learn, and if my name is on it, I never want it to fail," says McGrew.
See more of Dan McGrew's work at danmcgrew.com.