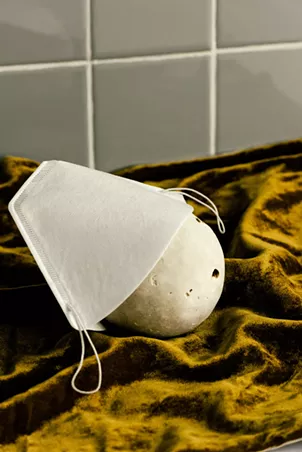
The New York Times Company
BERLIN — As the wave of coronavirus infections broke over Europe in March, causing reserves of medical supplies to disappear, German authorities made a nationwide appeal: More safety masks were urgently needed.
At Melitta, the company that pioneered the paper coffee filter, inspiration was close at hand.
“The ergonomics of the thing, the fact that the filter fits exactly over mouth, nose and chin is so unbelievable that you might call it a gift from heaven,” said Katharina Roehrig, a managing director at Melitta, which is based in a small city in northwestern Germany.
Melitta has a 112-year history with coffee filters. The company also owns Wolf PVG, which has produced air filters and vacuum cleaner bags for decades, providing valuable knowledge and a supply of the three-ply microfiber needed to make masks to a hospital standard.
“Facing this particular challenge, we realized that we could produce the needed quantities at an insane speed,” said Roehrig — in other words, as many as 1 million masks a day.
Many masks that filter small particles using microfiber rely on material whose production has mostly moved to Asia. In the mad rush to secure the raw materials, politicians and businesspeople have made it their business to find a source.
The essential ingredient in many medical-grade masks is a filter made of nonwoven superthin fibers, formed in a process known as melt-blown extrusion. Since the pandemic, demand for so-called melt-blown fiber has skyrocketed.
For Melitta, melt-blown fiber is readily available: It makes its own, mainly for use in vacuum cleaner bags.
The coffee-filter-shaped masks are produced on the same machine as the filters found in grocery store aisles. Although they physically resemble a normal coffee filter, the masks are made from different material (making them unsuitable for brewing coffee).
The material, a triple layer of melt-blown and spun-blown microfiber, has a Bacterial Filtration Efficiency certification of above 98%, a value comparable to simple medical masks.
Once the mask is approved by the government as a medical product, the company plans to supply those most in need in their region and eventually sell the product to a broader market.